Meinl-Weston 45SLP F-Tuba, serial number 92259. Upon play-testing this instrument, I find that it is more comfortable and has a much sweeter response than what I expected from a large-bore piston F-tuba. MIRAPHONE is a trademark and brand of MIRAPHONE e.G. Filed to USPTO On Thursday, October 21, 2010, The MIRAPHONE covers Musical instruments excluding talking machines, wireless telegraph and telephone apparatus, namely, tubas, French horns, baritones, euphoniums, trombones, trumpets, alto horns, fleugelhorns, coach horns. German oboe 10:56 on Friday, November 11, 2005 (Manny) Posted by Archived posts. Has anyone ever heard of a Hans Kruel Tubinger, wood conservatory obe made in germany. Re: German oboe 16:45 on Friday, November 11, 2005 (Sarah) Posted by Archived posts. I`ve heard of.
- A blog about the oboe, music, learning the oboe, teaching, performing, and all of these intersections.
- Miraphone Tuba Mouthpiece. $135.00 $182.00. Germany, Miraphone builds fine tubas and other brass instruments, and also offers a complete line of tuba mouthpieces. These are made for Miraphone in Germany by noted mouthpiece maker Josef Klier. These numbers are shown in the second column if.
- Miraphone 1292 CC 5/4 'New Yorker' Tuba The Miraphone 'New Yorker' was designed by Miraphone with the cooperation of Alan Baer, Principal Tuba for the New York Philharmonic The Miraphone 1292 produces a focused, clear and extremely well in tune sound, which is ideal for all types of playing, from large ensemble to solo.
Looking to buy a new or used tuba?
There are A LOT of different brands of new tubas out there today and it's easy for me to understand why some folks are confused about what to invest their hard-earn dollars into. As a person who spends twenty or so hours a week playing tubas and another forty-plus hours a week repairing them I can offer what my experiences have been when attempting to determine which ones are 'keepers' and which ones to pass on by.
How a horn plays is only part of what should go into making a decision of which one to buy. Bright and shiny isn't all it's often cracked up to be. The silver and lacquer finished on tubas have gotten pretty good but it's what's inside that counts. The term 'fit and finish' is misunderstood by most of the tuba community and has nothing to do with how shiny an instrument is. 'Fit and finish' as described by an engineer (yes... I worked for almost forty years as an engineer) is the way parts are machined and how well they work with each other. Finish isn't the pretty lacquer but the precision finished surfaces of moving parts such as pistons and rotors. Most of the time these precision finishes involve grinding or lapping and are specified in 'micro-inch' dimensions.
Look a horn over for obvious visual defects first. If it looks good... at least the maker has paid a bit of attention to the final aspects of manufacturing. Play the horn while watching a tuner and check all of the open partials and the partials of each valve to see if the horn is in tune with itself. Of course... the overall intonation should be manageable within 25 or so 'cents' on either side of A=440. Once it is determined that the horn plays in tune and your chops can compensate for any problems... move on to the mechanical elements.
- Try swapping the pistons with each other. The horn won't play with a piston in the wrong hole but you will discover very quickly if there is a shortfall in the manufacturing tolerances. This is very important if you ever have to order a new piston for the horn. Pistons can be hand-lapped but being able to order one and just 'drop it in' can be very convenient. Failure to pass this simple test is a fair indication that the rest of the horn may suffer from poor quality controls at the factory.
- Rotate the tuning slides 180 degrees to see if the inner tubes still fit. Also... switch the slides with each other to see if the inner and outer tubes are consistent. Failure here is a fair indication that the quality control of the raw materials used in the horn are not up to specifications or quality standards.
- Check the ease of unscrewing and screwing the piston top caps off and on. Poorly cut threads can quickly become a big problem expensive to fix. Threads that are 'scratchy' are a clear indication that they were cut with dull tools or the materials are sub-standard.
- Piston port alignment is more difficult for an amateur to check and usually cannot be done simply by looking into the tubes with the slides out.
- For rotary valves... the fit and finish of the rotors to the housings is paramount. ALL of the diameters on the rotors themselves have to be concentric. This is another area that's difficult to check unless you are a skilled machinist. 'Scratchiness' in the rotors is a good sign that the precision finished inside are not up to snuff. In some cases this is just grit left behind from the manufacturing processes but if the condition persists after a couple of cleanings... you've got problems.
- Aside from the way rotors are machined (or not) causing problems... improper assembly is a major issue. The back bearing plates must be properly seated into the back of the rotor housings. It usually takes a qualified technician can verify this.
- Rotor alignment is very important and should be verified by looking into the actual rotor passages and viewing the alignment marks on the rear bearing plates and rotor shafts. I've seen many cases where the alignment marks were poorly done and didn't match what the rotor was actually doing.
- Availability of repair parts is a major concern of mine. The industry has moved so quickly in the last twenty years that there are thousands of tubas out there that cannot be repaired quickly because no stocks of repair parts were made. Another reason is the quality has not been to a standard where parts could be replaced easily. (refer back to my comments on 'fit and finish' to get an understanding of this statement.)
Not very many will understand exactly what I have described here. Others will simply ignore what I've said because it's very difficult to quantify the differences between a $3,000 tuba and one that sells for $10,000 to anyone without a manufacturing or engineering background.
So.... your repairman suggested that you scrap the old 'S' links on your German tuba in favor of the spherical connectors.
Although I've seen a few cases where the old paddle assemblies were totally trashed or missing altogether... the majority of times those old 'clunky' S-links are easy to repair. The most common problem is for the pin to be loose in the paddle arm. The pin shown below was originally threaded into a hole in the bottom of the paddle lever. The threads had become loose and over time the threaded portion of the pin flexed enough for it come to the point of breaking off. From the factory.... the pin is threaded into the hole and tightened. Then the pivot tube is put over the pin and the washer goes over the end of the pin. The pin is peened to hold the washer and tube onto the pin. To do this repair the peened of the pin has to be ground off to free the washer. The tube can then be slipped off the pin. Next the hole in the lever is cleaned up and retapped. I usually use #4-40 threads. Drill out the lever arm with a #43 drill (closest fractional size is 3/32') and then tap the hole to #4-40. Next you'll have to find a piece of rod that will fit the tube on the linkage. In this case... the best choice I had is a piece of .118' rod... probably a rod from a saxophone. When doing repair work a person needs a hoard of odd parts and many sized of taps and drills. Also use a die to thread the end of the rod. Screw the rod into the hole and use silver-bearing solder to make sure the pin never tries to back out. I use 'Stay-Brite' because it is still a low-temp solder but is ten times stronger that conventional tin-lead solder.
Here is my 'go to box' for parts for linkage repair. Yes.... those complete assemblies in the foreground are of Asian manufacture. They are a good valve but the older 'S'-link European paddles are still my favorite.
OK. The pin is now soldered into the paddle arm. Grind off the threaded end so it's flush with the opposite side of the arm. Slip the tube of the link over the rod and mark the rod about 1/8' past the tube. This will leave room for the washer and a bit left over to peen to hold everything together.
Assemble the washer and use a small hammer to lightly peen the sharp edges of the pin until the washer comes very close to tightening up against the tube. I think perhaps the factory originally used a small orbital riveter to do the job but a hammer works well. Just don't overdo it because there is some risk of either bending the pin or making the assembly too tight. If you bend the pin you'll just have to start over. If the assembly gets a little too tight it can be loosened by placing the perpendicular tube on a small anvil and rapping the center of the peened pin. Here's where a couple of small 'raps' are much better than using too much force!
Finally.... here's the repaired paddle assembly back on the horn. The total time for the repair was probably less than the time it took for me to take the images and write this article. Honestly... this is a 1/2 hour repair and is something that any repairman should be able to do with just a few basic machine skills and good hands.
This was a 'project' to create a four valve version of a Yamaha YBB-103.
These are great little horns but are no longer made. Even the parts have washed out of the system. I don't know why Yamaha didn't make one with four valves. The horns play very well and have a large sound for such a small horn. The pistons interchange into any of the casings but they aren't available any more, either. Below are a couple of images of the valve section before and after modifications. I usually use a #2 casing from a donor valve section to create a 4th valve but in this case I cut the #3 loose and fit it to the other three valves.
OK. Most of the 'figuring out' is done. The valve section is back together and attached to the main body. Tomorrow I have to devise the 4th valve tubing wrap and the horn will be finished.
Ok... the next three images are of the horn that Yamaha SHOULD HAVE built instead of the 'kiddie' three-piston one. Note that there are TWO main tuning slides and TWO 4th valve slides and that the slides for all of the tuning slides are accessible from the top. The horn plays great and I can't wait to see how it performs in a rehearsal in the morning. If all goes well... I'll use it for Dixieland gig Saturday evening.
Here's another 'quickie' project!
I've owned an Alphorn for a couple of years and thought several times how it might be to make it chromatic. This Alphorn came to me missing the extension joint to change it from F# to F so I made a tunable segment that plugs into the mouthpiece receiver. I use a 6 1/2al trombone mouthpiece on the horn since I spend most of my time in the lower register playing in an Alphorn trio. The maker is Otto Emmenneger and I think the horn was made sometime in the 70's. The first chore was to scare up a cluster from an old 'Continental' (Conn stencil) F horn. On the left end of the cluster is an adapter that fits into the receiver on the Alphorn. On the right end is a trombone receiver.
In the next three images you see the finished rotor section. Other modifications to the cluster only included a bar to stabilize the slides and a bar to serve as a thumb rest under the keys. I also reversed the slides and 'flipped' the valve section to make it right-handed. Yes... intonation is very good!
Play conditioning an Ophicleide...
Below is an image of how I received the horn. It's pretty typical of other French-made ophicleides I've seen. The plain engraving on the bell reads 'Beckner Aine A Paris'. This one's had a pretty rough life but then again... it's probably around 160 years old. The bell is in pretty good shape. The wire is not broken but there are three small splits in the rim... which I will wrap patches over. One key is missing completely so I will have to fabricate a new one. Having scrap saxophones around comes in handy! When this one is finished, it will have leather saxophone pads. The piece of leadpipe shown was sent with the horn but does not belong on it. The owner just sent it along in case I wanted to reuse the receiver. I will have to add a piece to the leadpipe before adding the new receiver. The new receiver will be one to take a regular-shank tuba mouthpiece. These horns respond well in the lower register using a tuba mouthpiece and I will also include an adapter to use a euphonium mouthpiece so it will play well in the upper register. I don't know the pitch yet but I'm guessing it's a Bb. The bocal is longer than the last one I rebuilt... which was a C.
OK... Below, it's all apart and ready for the serious work. The small conical section is 'brickly' to the point it will have to be complete replaced. There's no patching things when they get this bad. 'Brickly' brass is said to be caused by exposure to ammonia and similar chemicals. The areas that are the worst are where the play would have held the instrument while playing it. There is no sign of damage in the bottom bow or large conical section. Knowing I'll be replacing the small conical section... I've already removed all of the 'hardware'.
Hey! It's my 'lucky' day! I just happened to have a piece of .015' thick yellow brass that will do for the new conical section. A guy who works with sheet metal all day long could lay in out 'in the flat' but I find that the easiest method is to just build a wood mandrel using the inside dimensions of the part I'm replacing.
Having a Ferree's Z60 dent machine with lots of attachments makes it fairly easy to roll the brass into shape. Once rolled to shape the tube is wired and soft solder is applied to a lap-joint that's about 3/8' wide.
Below is a small conical section about ready to remount the tone holes and keys. Notice that the old bottom bow ferrule is attached to the left end of the tube. I made a slight alteration over how the upper end where the bocal fits is made. Originally... the tube tapered all the way from the top to the bottom without really allowing the slip-joint for the bocal to maintain good contact. I reused the original pinch screw collar but used a section of straight tubing that matches the bocal perfectly. This sub-assembly will be soldered into the top of the small conical tube.
It's time to mount the tone hole chimneys to the small tube. It's just a matter of measuring the old tube and putting the chimneys in the same location. The split in the bocal receiver is mounted in line with the seam on the back of the tube and the chimneys are attached in the same relative position as original. A small hole is drilled in the tone hole location to aid wiring the parts together. The tone hole will be opened up with a Dremel tool later.
The tone holes have been 'cleaned out' and the next step is to reattach the key saddles. The middle key was missing completely. The finger paddle will be located between the other two keys. Making the key will be pretty straight-forward so I'll just put the small section aside and take a look to make sure there aren't any problems with the larger tube.
It's a good thing I took a closer look at the larger tube! I decided to unsolder the tone chimneys in order to make the dentwork easier and discovered leaks under three of them. Sometimes it's just better to take everything apart to make sure there aren't any hidden problems. Working with the chimneys used on these horn is quite easy since they are heavy brass (or maybe bronze) castings and keep their shape pretty good despite years of being bumped and banged.
Here we go! All ready to start putting the rest of the hardware back on. I did discover two cracks about two inches long in a 'brickly' area just above and to the right of the diamond-shaped solder mark. The rest of the large tube is solid so I'll just apply a patch to the area later. The cracks don't seem to be leaking but the patch will eliminate any problems 'down the road'.
There were three small splits in the bell rim but the wire was not broken. I applied three small patches that wrap around the rim. The patch is on the 'brickly' area I mentioned in the above pictures and now I'm ready to start putting the key saddles back on.
All the key saddles are back on and the bottom bow has been reassembled. The 'meat cutter' on the bottom of the bottom bow was missing so I replaced it with a piece of sousaphone bow guard. The ornate upper brace has been reattached. The picture on the right shows the large patch that has been applied to cover several cracks. The patch is just behind the attachment loop. I discovered two more small cracks less than 1' long in areas that are non-structural and filled them with silver-bearing solder. Silver-bearing solder still has a low melt point of about 450 degrees like conventional soft solder but contains 3% silver to make it about ten times harder than lead/tin solder. The REAL benefit here over 33% silver solder is that the low heat required is less apt to make the already 'brickly' brass worse.
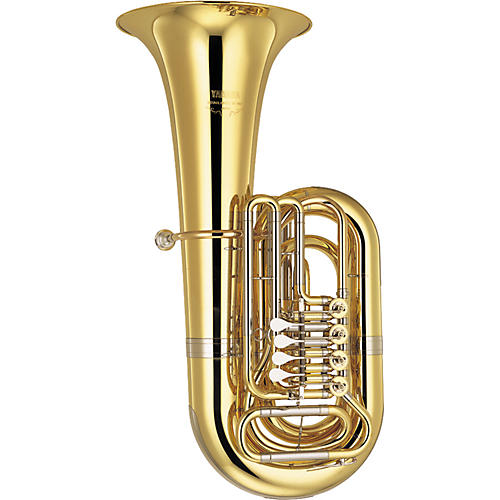
OK. It's time to start working on that missing key. I've parted out several bari saxes over the years and this box of 'goodies' comes in handy. I selected one key from which to salvage the right size key cup and another key for the body and paddle. A piece of tubing was taken from yet another key. I also had to make several of the pivot screws. One key was wired onto the horn and another had a nail through the pivot tube. I also have an abundant supply of old sax pivot rods and selected some that were .104' diameter and already had the correct threads on them.
The image below shows the assemble new key. The tube is hard soldered to the key body and I used silver-bearing solder to attach the key cup to the body. I then bent the body 90 degrees.
All that is left to do on the ophicleide is to clean it up, install the key springs, and the pads. Some of the pivot pins are yet to be cut to the proper length and the decorative thumb-screw mounted to them.
OK. Below are a couple of image of the finished ophicleide. I make a couple more 'tweaks' after these pictures were taken to make the horn a little more 'user friendly'. The mouthpiece is now a little lower angle and the top hand hook was moved radially toward the front to get better access to the left hand keys.
Rebuilding the stems on old Alex rotors
I had an old Alex come to the shop last week. It was suffering from a variety of problems including badly worn stop arms, dents, a few splits, and generally in bad shape. Initial 'toots' would not center and the horn was basically unplayable. The first thing I had to take care was figure out a way to reconstruct the stems and the holes in the stop arms. They were so 'wallowed out' that there was at least 15 degrees of 'play'... virtually impossible to get a descent valve alignment.
Above you can see the condition of the shafts and the holes in the stop arms. Originally, the shaft was three square sides with the fourth side having a 'peak'. The third rotor was the closest to correct. It would have taken many hours of hand-work to build up the shafts with braze and work it back down with a file. Even tougher would have been to restore the marching internal shape on the stop arms. I recalled that my King 'pit model' rotary tuba has small dowel rods as keys to align the stop arm to the shaft. Sooo... I set out to modify the Alex parts.
In the above image.... I turned the portion of the rotor shaft where the stop arm fits just enough to 'knock off' the sharp edges. Then, I cut four short pieces of brass tubing to slip over the shafts. The inside diameter of the tubing is about .188' and the outside diameter is about .210'. The exact sizes aren't really relevant as long as everything slip-fits together. I used silver-bearing solder to assemble the tubing to the shafts. This type of solder is about ten times stronger than traditional lead/tin solder and only contains about 3% silver.
Next... I drilled a holes in the stop arms that were a tight slip-fit over the new surface on the rotor shafts. Orientation is not important yet. The holes for the keys will be put in next.
It's time to assemble the valves and key the stop arms to the rotors. The alignment marks on the back bearing plates and rotor shaft were verified with a borescope. I never rely completely on the alignment marks! Note that there is room for final adjustment by trimming the bumper that will be inserted into the stop arm. Once the rotor to stop arm orientation was established, I drilled a 1/16' hole... splitting the diameter between the stop arm and the shaft. Where the hole is located on the diameter is not important because all of the rotors and stop arms are stamped with a number so they can be matched up again. When a horn is taken apart, it's always a good idea to find the assembly numbers. If no numbers are present... I use a pin punch to make one, two, three, or four marks. In the picture on the far right, you can see the 1/16' dowell rod in place in a different rotor. Note that the location is not the same.
There you go! All ready for the bumpers and to put the linkage assembly back on. Note that I also had to make a new stop pin for rotor #4.
To follow are a few more pictures of the Alex...
And finally... the clockwork spring mechanism and linkage. Note that these have user-adjustable tension. The thumbwheel appears to be missing from the #1 unit but hopefully I'll be able to fashion a replacement.
Need a neck for Conn 12M bari sax?
A couple of years ago, I took a Conn 12m bari sax in trade for some school repairs. The problem was that the school lost the neck (imagine that!) and Conn/Selmer never took the time to offer a replacement neck after they quit manufacturing the horn. So... the sax layed on a shelf in my shop for a looong time waiting for a neck to show up. I finally got tired of waiting and decided to just make a neck out of available parts. I had a Bundy bari sax neck and parted out the sax a while back for parts for another project. The Bundy neck look 'sort of right' but the male tenon was only about .881' diameter while the receiver on the Conn was about .979' diameter. The good thing about the Bundy neck is that it also has an octave key on the neck. The octave mechanism on the Conn is about .800' to0 high to mate with the key on the neck. But... since from the pictures I've seen, the Bundy neck is a little shorter than the Conn... a riser of about .800' would work OK. Here's the piece I made:
The brass piece is soldered into the Bundy neck and fits nicely into the Conn receiver. Intonation is even over low, middle, and high Bb. All that was required was to lighten up the octave key spring a bit to balance the mechanism.
I 'retired' an important tool today!
A few of you who have visited my shop may have noticed an ugly, burned, taped-up cardboard box on my work bench. Some repair guys have fancy sandbags and special fixtures for holding objects while they are being worked on but that grubby cardboard box has been my 'third hand' for probably ten years or so. That box has finally reached the point where it's just not cost-effective to make any further repairs to it and it's been given an appropriate burial in the dumpster! It has been replaced by the new box on the right. And yes.... that Conn 28K (Eb) sousaphone was the first instrument to be propped up by the new box.
An interesting Buescher tuba...
I ran across this horn at the Summer 2011 'Windjammers' meet at Oskaloosa, Iowa. It's a custom Buescher owned by Bob Adams. The horns was built in 1928 for a member of the Cincinnati Symphony Orchestra. The VERY interesting thing about the horn (other than the valve cluster layout) is the location of the leadpipe. You can see that it exits to the rear of the horn on the opposite side of the bell from conventional leadpipes. The owner has the other leadpipe and it looks like it was made to use with an upright detachable, which he does not have.
'Jumbo Summit'
The three Conn 'Jumbos' pictured below mysteriously appeared in a grassy area in Pentwater, Michigan around 6:30pm on Thursday, July 16, 2009. My goodness!.... that one on the left certainly is shiny, isn't it?
Oh, oh... wait, wait... those three 'Jumbos' weren't really abandoned in that vacant lot after all! Introducing the 'players'. From the left: Andy Loree from Silver Lake, Michigan... Dan Schultz from Newburgh, Indiana... and Jonathan Hodgett of England. The three were present to play in concert with The Pentwater Civic Band on Thursday, July 16, 2009. OK... does anyone else have pictures of three 'Jumbos' together? We're thinking that this might be the first time since Sousa's band quit touring in the 30's.
Cerveny 'Kaiser' Tuba
Here's a fun 'little' tuba! .820' bore with a 19 1/2' bell. Probably made between 1910 and 1930. The serial number appears to be 37C9L. Funky short stroke finger paddles with adjustable tension clockwork springs.
And now... introducing the Conn 'jumbo'. I don't need to say much about this massive sousaphone. It tips the scales at 42 pounds and has a 28' bell. This one's satin gold and in good shape for being a 1928 horn.
Alexander or B & S stencil??
I came across this rotary tuba that has me a bit befuddled. It looks very similar to some of the GDR B & S stencils (aka Sonora, Carl Wunderlich, & Gerhard Schneider) that I've seen but there are some characteristics that are different. Someone suggested that it might be an Alexander. What does the TubeNet 'freak jury' have to say?
Note the large 'keel'. The GDR B & S tubas seem to favor just a bow guard wire and no keel. The waterkey has a flat spring.
The attachment plate for the harness rings are shaped like B & S - built tubas, but I've not seen a round ring before. The B & S horns have a ring shaped to fit something like a rifle sling.
The 'twist' in the #3 valve tubing is like both the Alexes and the B & S stencils. The 4th valve wrap is also like them. Also, the large ferrules are like both Alex and B & S tubas.
OK.... it's time to vote. There are no serial numbers or markings anywhere on this horn. The bore is 19mm. The bell flare has no garland and is 16 3/4' diameter. The throat where the bell stack enters the bow ferrule has a circumference of 15' and is very close to the bell of a Mirafone 186 in all respects. Another interesting thing.... this horn had the wrong back cap on the #1 rotor. One off of a Meinl 20/25 fit fine. The consensus is that this horn is a B & S stencil. It's back together now and in a new home in Washington State.
Olds/Reynolds upright tubas
Some folks get confused talking about the Olds 0-099 tubas and the Reynolds tubas that were very similar or the same. There were small and large Olds and Reynolds tubas. Below is a picture that demonstrates the huge difference in the sizes of Olds & Reynolds tubas. If I remember correctly, these were both Olds tubas:
Double-belled Euphoniums (pictured below)
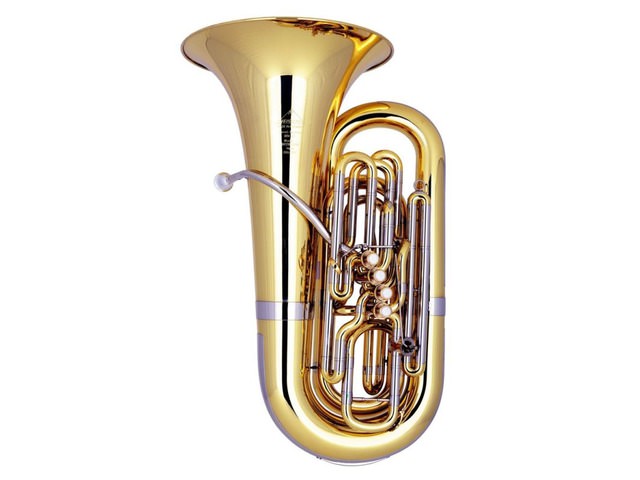
These instruments are often misunderstood. They can only produce sound through one bell at a time. And... the pitch is the same whichever bell is being used. Only the timbre changes. The larger bell sounds like a typical euphonium while the smaller bell produces a more trombone-like sound. The tubing leading to the smaller bell is more tubular and less conical than the tubing on the larger bell side of the horn. The DB euph on the left is a Conn. It has three top-action valves and a change valve on the side to divert the sound to the smaller bell. 2nd from the left is a Buescher. the 3rd one is a Martin. and, the one lying on the floor is another Buescher with a small upright bell (not original). The front-action horns have a 4th valve that can be operated by the right hand 'pinky' or by the left hand index finger. Nice little family! Oh yeah... the BIG tuba on the left is my Bohm & Meinl Marzan... soon to be joined by a Marzan 'slant-rotor' sister.
Mic Holder for Sousas and Tubas
Here's a homemade microphone hold that works on all sousas and tubas with bells ranging from 13' up through 30'. It's made from pieces of small telescopic tubing to the three 'legs'. They are soldered to a 7/8' ID piece of tubing in the center by using using tuba brace flanges. At the outside, the 'legs' pass through pieces of rubber that are split to go over the tuba bell flare. I like to use a cordless lapel mic setup and just push the mic (with it's foam 'breeze guard') to the tube in the center. The pre-amp and transmitter can then just be held in place with rubber bands or tape anywhere on the horn. The mic holder is shown in place on a King fiberglass sousa.
Harv's 'Groundhog Caller'
Harvey Hartman (Harv's Happy Horns) sent me the following pictures of his 'Groundhog Caller'. As you know, groundhogs are a big deal in Pennsylvania!
Here's a REAL French horn:
Brass repair is brass repair. This little goodie is a French automobile horn. To make it blow, a rubber wheel on the air pump engages the engine flywheel. It plays in D#! I could have used a bell screen like that on my sousa in a Mardi Gras Parade a few years back!
Linton contra-bass clarinet
Yeah.... I know. It's not a tuba. It's STILL interesting! Like one of the TubeNetters says.... 'welcome to Heaven, here's your tuba.... welcome to hell, here's your saxophone'. Well, the best description can come up with for this creature is 'Polish Saxophone'. Actually, it's a Linton. Not really made by Linton (the oboe and bassoon folks)... but made by ORSI (Italian) for Linton probably sometime in the 70's.... during period when instrument makers were all searching for the 'bigger and better' instruments to sell to school band directors. This one was a dreadful failure. Partly because no one ever bothered to make reeds for them on a production basis. The reed needs to be 15/16' wide to cover the rails... a full 1/8' wider than the widest commercially available reeds made for bari saxes and bass clarinets. According to Mr. Linton, there were only about 40 of these things made. I know of two of them. The rest have probably gone to the scrap yard or maybe on the wall at the neighborhood 'Fridays' restaurant!
Below are a couple of pictures of the mouthpiece. It's compared with a bari sax mouthpiece and a bari sax reed. Note that the tenon that fits into the horn is over 2' diameter. There have been some unsuccessful experiments to adapt a regular bass clarinet or contra bass clarinet mouthpieces to this horn. I've been experimenting with making a plastic reed for the horn. Anyone care to give me a hand? Remember... I'm a tubaguy. Woodwinds aren't really my thing!
Meinl 33
Reynolds Tuba (TB-09??)
Mirafones
At first glance, I thought both of these horns were Mirafone 186's. The one on the left is serial number 25XX and the one on the right is serial number 93XX. The one on the left has a bore of .780', a 16 1/2' diameter bell and is indeed an old-style 186. The horn on the right has a .740' bore and a 14 3/4' diameter bell. Both horns share the same wrap configuration. I've owned 182, 183, 184, and 186 Mirafones but have never seen a 185. Is the horn on the right a Mirafone 185? It's more-or-less been confirmed that the tuba on the right in the pictures below is a Mirafone 185 BBb.
How NOT to wear a sousa!
The guy on the left is wearing his sousa fairly correctly... with the bell assembled perpendicular to the main body wrap. That goofy guy on the right has assembled his sousa with the bell just about parallel with the main body wrap.... very uncomfortable to wear and it's almost impossible to see around the bell. I had a sousa come into the shop today (7-23-07) and the band director complained that the bell covered the student's face and he wants the bell crook unsoldered and revolved a bit to tip the bell up so the student can see. I explained that they were putting the bell on wrong but he insists that it has to be that way to 'look centered' when marching with other sousaphones. The 3rd picture was taken AFTER I unsoldered the body elbow and rotated it about 35 degrees to pitch the bell up so the player can see. The customer is always right! 'Scuze the blue exam gloves. I always wear them in the shop to keep my hands young and supple! Note the similarity between the most recent picture and My TubeNet avatar.
Here's another 'interesting' tuba:
This one is a Cerveny... serial number 26666... imported and sold by Georgi Vitak at 4663 Gross Avenue in Chicago sometime between 1907 and 1923. The address of the Vitak music store noted on the badge is significant because Vitak was at that address only during those years. Gross Avenue is now McDowell Avenue. The badge on the horn mentions Expos from 1889 to 1893, but the horn couldn't be that old because of the address. The bore is 21mm (.827')... the bell is 19 1/2' and the overall length is about 41' It's pitched in BBb. The girth of the bell throat where it enters the bow ferrule is 19' (or 6' diameter)... quite a bit larger that the rotary tubas of today. Of particular interest to me is the LOOOONG leadpipe, the configuration of the main tuning slide, and the 'openness' of the wraps. The horn plays 'OK' but is in need of a complete rotor overhaul. Don't call me wanting to buy this horn. It went back to the owner.
'Kicker' on Besson Prestige
Above is a picture of a 'kicker' installed on a Besson Prestige. Kevin Powers makes the parts. It takes a bit of doing to fit up the paddle and mount the bracket but the installed unit is quite functional. The real trick is to get that darned main tuning slide aligned PERFECTLY and honing the slide tubes for a nice sliding fit. This is not something you should attempt to do in your home workshop. As you can see, on this particular horn, there was barely enough room to retain the 'grime gutter'. The 'kicker' allows about a 1' extension of the tuning slide.
Willson DEG BBb 'Commuter' tuba
This is a cute little horn that was originally marketed as a student horn under the moniker of 'commuter'. It came with two detachable bells... one brass bell that was to be left at school for concerts... and a plastic bell that could be taken home. Then, all the student had to carry to and from school was a small case containing the tuba body. The horn is about 32' tall, has a 15' bell, and a bore of about .640'. This horn is bright silver plated. The bell pictured is actually salvaged from an old Holton Eb tuba but is very close to the size of the original bell. The horn was also originally a convertible horn with two leadpipes... one for concert configuration and one for marching. Two pictures are below.
King Stuff...
Just added the picture below... I'm not one to leave ANYTHING alone! The below picture is of a King (1241/2341.. whatever!) that I 'warmed over' on February 20. It WAS an old style horn. I moved the #1 tuning slide to the top and added an Amado waterkey. Then, I extended the bottom 3rd valve tuning slide (thanks to a King sousa) and got rid of the double-wrap at the top of the #3 circuit. It's starting to look a bit like the modern version of the 2341... except for the detachable bell. I also put on a 'manly' sized thumbring! Oh yea... the leadpipe is new, too! Mike Self... this is the one I got from you!
Two King tubas are pictured above. The top one is a model 1240 from around 1932. It has a fixed bell. I was tinkering with the idea of assembling the leadpipe and tuning slide with the slide pointing 'up' so I can make tuning adjustments 'on the fly'. I decided to just put the horn together the way the factory made it because I was concerned that condensation would not drain properly with the slide pointing up. Another thought was to install a straight leadpipe and adding a little tubing AFTER the valveset. Know what??? ... After putting the horn back together and giving it a toot, I found that tuning adjustments aren't really necessary! This is an incredible horn for a three-valve tuba!
The bottom picture is a detachable bell King. The valve section is very similar to the model 124o but the leadpipe configuration is different. The modern version of this horn is the 2341. What is the model number of THIS horn?
OK... this has been discussed and I'm ready to offer the following picture and my personal opinion:
The above picture shows four Kings that I currently own. From left to right...
Model 1235 Eb (4th valve was added recently) sn 178502 (1935)
Model 1240 BBb - sn 152446 (1935)
Model 2340 BBb - sn 415755 (1966)
Model 2341 - sn 274107 (1945)
Below are two images that are currently being used to advertise the King 2341. It's fairly obvious that even King is confused about how their horns look! The image on the left more favors the 'old style' 2341's as shown above. The image on the right appears to be more 'real' in terms of what the 2341 actually looks like today...
What does all this discussion about the kings come to? Well... It's MY OPINION that there were NO model 1235 (Eb) tubas made that had a detachable bell. All of them had fixed bells. All of the 1235 (Eb) tubas that I've seen had the tuning slides in the leadpipe. There is a real mix of 1240 and 2340 tubas out there.
The 2340 tubas incorporated a series of manufacturing changes but still retained the same model number. None of them had tuning slides in the leadpipes but none of them had fixed recording bells. Some of the later ones were sold with the fixed upright bell only. A major change took place in June of 1980 and did away with the detachable bell completely. The leadpipe was also changed to incorporate a bell with a 'quicker' taper. The leapipes of the 2340/41 tubas made before June 1980 and after June 1980 will not interchange.
Confused??? Yeah... it's confusing. It's further confused by the fact that United Musical Instruments (UMI) already owned Conn and then bought King... closing the Conn plants and moving all of the tuba production to the Eastlake, Ohio plant... creating some 'composite' horns like the Conn 15J and the King 1140.... which were actually the same horn after 1985!
Whatzit?
Below are three pictures of a hybrid that came through the shop a while back. It's obviously a Conn body 'cause it says so on the bell! It turns out that the valveset is built of parts from Selmer/Bundy/Buescher tubas. Nice horn.
Whatzit?
Email me if you have any ideas. BBb. The bell is 21' and the bore is .860'. The horn on the right in the following pictures is my Mirafone 186... for a good size comparison. I originally thought the horn might be an old Alexander, but the consensus from the TubeNet 'freak jury' is that it is most likely a Bohland & Fuchs. If you have any different ideas or additional information please drop me an email. I haven't found any serial numbers, names, or other ID of any kind.
Above left is an image of the valve section. The image on the right is one of the attachment points showing the shape of the badge backplate.
The bell rim is 'interesting'. It looks original. Instead of a wire and kranz (garland) that are seen on many German tubas, there is a half-round silver reinforcement soldered or brazed to the rim of the bell.
The rotor section is above.
The above style brace appears in a couple of places between the cluster and the main branches. The brace below is incorporated into the tuning slides.
This image shows the details of the stop arms and stop pins.
Above is the receiver for a LARGE European shank MP... with an adapter that I got with the horn.
Email me if you know what this tuba is. UPDATE: This tuba was most likely made by Bohland & Fuchs. It's now living in Kansas!
The New Kia 'Rondo'
Yea, yea.... I know! I'm the one who always said 'get a Chevy'. What can I say?! I bought this new car on December 5th and I think it's just great! Us tuba guys are always worried about transporting our horns. This Kia 'Rondo' is a brand new line for 2007. It's the largest of a series of five-door automobiles before getting into the mini-vans. It has a five passenger seating with an optional rear seating to add another two small people. I bought the five passenger version.
The image on the left above shows the Kia configured for five passengers and there's still plenty of room behind the rear seat for my Miraphone 186 in a gig bag, my music stand, and the grocery cart that I haul the horn in. The image on the right shows the rear seat folded down so there's plenty of room for percussion equipment owned by the friend I'm picking up before a gig today.
My first impression of this auto after only two days of ownership is that it is an outstanding vehicle. I've been looking for a car that has the utility of the old station wagons of the 60's and 70's and I think this one will fill the bill.
Conn bass 'bone
Serial number 41 361235. 10' rose brass bell... .600' bore valve section. What's the model number? Got it! It's a 112H. It just has a lot of miles on it for it's age! There's an interesting story about this horn.... As you can see in the below pictures, it is missing all of the rotor linkage... including the mounts that are soldered to the horn. Conn-Selmer had the parts but didn't have a clue how they were assembled. Several calls to the Eastlake factory got me nowhere. I finally bought the parts and 'stumbled' onto a good illustration on the Jupiter website. Apparently this trombone was not made by Conn and is actually a knock-off from the same folks who make the Jupiter version. Maybe Chinese???
Above is a YBB321 that almost survived a pep band! It appears as though some kid (or stupid adult alumni) thought the combination of mouthpiece and horn made a great drum! Below is a picture of the repairs to the knuckles. Some of the knuckles were straightened and some were replaced with parts available from Yamaha. This is an old style 321 (serial number under 100,000). The new knuckles are actually parts for the new style production but can be used by cutting off the old knuckle, swaging the new knuckled, and soldering it over the old stub. The repair is not quite finished, but you get the idea. Sometimes the things that look the worst on a horn can be among the easiest things to fix. Odly, the valves were not damaged with all the beating and banging.
Miraphone Website
So... you think you should trust FEDEX with your brand-new tuba? The seven bells tuba bells pictured above made it half-way around the World to Florida just to be demolished by FEDEX on the short trip to Indiana!
Poor little storage shed two days after putting 509 screws in it! Due to a little puff of wind directly out of the north. I just flipped it end-over-end to where it came from and put in some new anchors. Not much damage except for a few small dents... and I KNOW what to do with dents!
Miraphone Serial Numbers
Pictured above is a Mirafone BBb 186 (left) and a Meinl 25. Note that the valve sections are very similar but the Meinl 25 has a much larger bottom bow and bell.
Page last edited on November 18, 2015